SUMMARY
Fiber-reinforced polymer (FRP) composites have a wide range of use in military applications, including portable shelters, aircraft structures, ship structures, and some ground vehicle components. These composites bring major advantages over metals, including resistance to corrosion and lighter weight for increased mission range. However, they present a very different fire risk scenario (chance of fire loss) than what is seen with metals. Specifically, they are not easily extinguished with foams, can structurally fail well before the fire grows large, and can present survivability and vulnerability challenges. This article will focus on how composites burn, give an overview of known hazards and their effects on equipment and personnel, describe possible ways of addressing composite flammability. Best practice firefighting measures for dealing with composite fires will be discussed, along with fire protection measures compatible with composites. With this information, readers will be better equipped to deal with composite fire risk scenarios and can start using some of the known fire protection measures to design fire-hardened military equipment.
INTRODUCTION
Composites, materials composed of more than one material, are increasingly used in military applications due to their high performance over existing single-material components. Many of us are familiar with carbon-fiber epoxy composites used in high-performance sports cars or golf clubs and even with epoxy + fiberglass composites in circuit boards. Composites can be made of a wide range of materials, including carbon-carbon composites (used for brake pads and reentry shields), ceramic matrix composites (reinforced ceramics for very high-temperature applications such as engines), and metal matrix composites (two different metals, not alloyed, used in high-performance applications such as landing gear). One of the more common composites used today are FRP composites like the epoxy/carbon fiber and epoxy/ fiberglass materials just mentioned. The polymer in the composite can be highly varied depending upon the synthetic polymer used. The fibers can also vary, from the common fiberglass and carbon fiber to Kevlar, silicon carbide, quartz, metal, and other strong fibers in select composite applications. For military applications, FRP composites are present in ships (structure and bulkheads), aircraft (fixed and rotary wing), portable hard-wall shelters, some handheld military gear and weapons, electronic components, and ground vehicles (structural and nonstructural parts and spall liners). FRPs are used because they bring lighter weight (improved mission range), good mechanical properties, resistance to corrosion, and other benefits that may not be achievable or practical with existing metal or ceramic materials. Some well-known examples of polymer composites in military use today are shown in Figure 1.
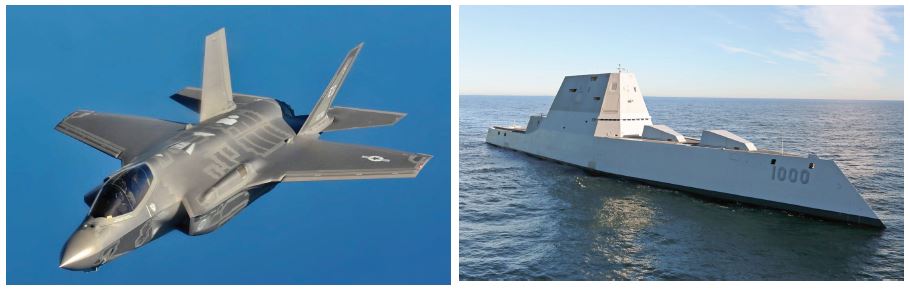
Figure 1: FRPs in Military Applications (Sources: [Left] U.S. Air Force MSgt Donald R. Allen and [Right] General Dynamics Bath Iron Works).
FRP properties are prized in the civilian world, where some of the same military applications are mirrored in ships, aircraft, ground transportation (trains, subway, cars, and trucks), and electronics. FRPs are also used for building materials, wind turbine blades, electronics, and train/rail/subway cars. There is a continued desire for new uses for FRPs in civilian markets due to their performance and cost benefits. While FRPs bring many advantages to their widespread use, they do have limitations. Temperature is their main limitation [1]. Specifically, all polymers in FRPs have a “glass transition” temperature where the material begins to soften and deform with force applied.
This happens before the material melts and is effectively the “use temperature” for the material. The use temperature will vary depending upon the chemistry of the polymer used to make the FRP. Some FRPs can be used up to 300 °C (572 °F), while others will begin to notably soften in temperatures as low as 40 °C (104 °F). Certainly, metals have use temperatures and performance limits, but usually, metals can withstand heat much better than FRPs. Along with this temperature limitation is a key survivability/vulnerability concern, which is how polymer composites burn. This limitation is very different than most military-grade metals. Some metals can burn quite spectacularly (e.g., magnesium alloys). But it is how FRPs burn when exposed to fire that presents challenges from the perspectives of force protection and structural durability, when the FRP may structurally fail early in a fire and lead to catastrophic losses. While these thermal properties can present notable survivability and vulnerability threats for military equipment, they can be overcome and shielded. This article discusses known historical events where FRPs in fires caused structural failure and military equipment loss. From those examples, details on how to protect FRPs against fire will be discussed, including their specific hazards and how military firefighters should approach FRP fires.
EXAMPLES OF COMPOSITES POTENTIALLY EXPOSED TO FIRE IN MILITARY USE
Fire protection engineers look at the fire hazard (damage caused by a fire) and fire risk (chance of fire occurring) to create a fire risk scenario. Once that fire protection scenario is defined, it becomes possible to protect against the fire in that scenario should a fire occur. Fire risk scenarios are not universal, and the fire threat for an aircraft will be different than for a ship or a ground vehicle; the same is true for FRPs.
Our first fire risk scenario begins with fires on ships. There are two examples of FRPs in naval fires that have led to complete loss of the ship—the Royal Norwegian Navy minesweeper “Orkla” and the Indonesian littoral combat ship “Kri Klewang” (to be discussed in the following paragraphs). These examples serve as a warning to not ignore FRP fire behavior in typical naval fire risk scenarios.
Fire onboard ships is not a new phenomenon and has been thoroughly studied since the dawn of naval surface warfare. When navies of the world moved to metal hulled ships, the main fire risk scenario of a wooden ship “burning to the waterline” and capsizing was replaced by compartment fires due to fuel spills and munition-induced damage. However, with the advent of composite hulls, the scenario of the hull burning has returned but in a somewhat different manner. In two reported cases, ships with composite hulls were involved in fires. In both cases, the ships had notable structural fires while burning, resulting in the ships capsizing and sinking.
The first example is the Royal Norwegian Navy minesweeper “Orkla,” which developed a fire in a propulsion room [2, 3]. As the composite hull and structure of the minesweeper ignited, it quickly overwhelmed the firefighting crew who were forced to abandon ship. The ship burned for just over 24 hours before capsizing, breaking apart, and then sinking. A post-mortem analysis found that the fire suppression system on the ship failed, indicating that due to the flammability of the composites that made up most of the ship structure, additional passive fire protection for the composites was needed.
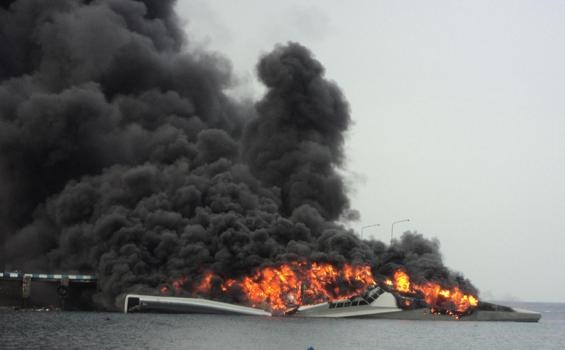
Figure 2: In September 2012, the Indonesian Navy’s Kri Klewang Suffered Major Fire Damage (Source: http://www.tribunnews.com/regional/2012/09/28/kapal-siluman-kri-klewang-…).
Another example of a composite ship catching fire and resulting in total loss of the ship was the Indonesian littoral combat ship “Kri Klewang.” This ship caught fire due to an electrical short while docked and getting fitted for sea trials (see Figure 2). Again, the fire protection system did not activate (it had not yet been installed). The fire was quite large, and the entire ship was lost [4, 5]. Note in both cases, the fires were so intense that ship firefighting measures were not enough to overcome them. Clearly, both incidents support the need for secondary fire protection of the composites to ensure no loss of structure and, more importantly, that the fires do not get out of control from the beginning.
Acceptable secondary fire protection for composites can include using flame-retardant polymer in the FRP. Ceramic fiber fire protection blankets and wraps are commonly used onboard U.S. Navy/Coast Guard ships with composite structures as well as onboard civilian maritime ships with composite materials. However, these ceramic blankets have their own issues, such as installation/maintenance. But they are proven to work as a backup fire protection system in the event fire suppression systems and fire protection crews are unable to address the fire in a timely manner.
Another fire risk scenario for FRPs in military applications is in ground vehicles. Setting aside highly complicated fire risk scenarios such as incendiary and high-explosive rounds, compartment fires are a known fire risk scenario that can kill the crew of the vehicle if it gets out of control. In the past, halon extinguishers and self-sealing fuel bladders, combined with a mostly all-metal vehicle hull and interior components, would address most of the nonmunition-based fires in vehicles. More recently, high-performance FRPs are inserted into vehicles such as mine-resistant, ambush-protected vehicles, namely as spall liners capturing fragments from mines and other munition threats. Work conducted by this author, through U.S. Army funding, found that the composition of the FRP spall liner great affected its flammability [6]. In some cases, the spall liner’s flammability was low enough that the crew could grab an extinguisher and put out the fire. But in other cases, the flammability of the FRP was so high that a hand-held extinguisher was insufficient, and immediate exiting of the vehicle was recommended. Older technology S-2 glass + phenolic polymer FRPs showed very low flammability, while newer lightweight, ultrahigh molecular weight polyethylene FRPs showed very high flammability when studied by a cone calorimeter [7]. The cone calorimeter measures the inherent flammability of materials. The higher the heat release rate (HRR) of the material, the higher the fire hazard for that material (Figure 3) [6]. Both spall liners provide their expected protection against fragmentation threats, but only the phenolic polymer FRP provides low-heat release and fragment protection. This further supports the importance of understanding FRP inherent flammability and how selecting the wrong FRP can have unintended consequences from a fire protection perspective.
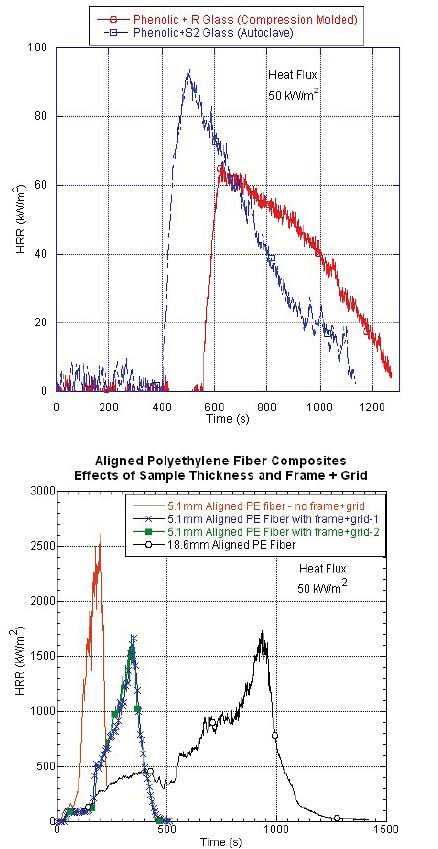
Figure 3: HRR Curves for Phenolic + S-2 Glass FRP Spall Liners (Top) and Ultrahigh Molecular Weight Polyethylene Spall Liners (Bottom) (Source: Morgan [6]).
The higher the heat release rate (HRR) of the material, the higher the fire hazard for that material.
A notable incident of how composites have burned in aircraft and some of their specific hazards that resulted in different firefighting measures occurred in February 2008. A B-2 bomber (mostly all composite; see Figure 4) crashed onto the runway shortly after takeoff, resulting in a large fire and complete loss of the $1.4B aircraft [8]. Since the aircraft was recently fueled, the tank likely exacerbated the fire upon crashing. The resulting fire and guidance from aircraft manufacturers on how to put out FRP fires are worth discussing as well as the hazards to ground crews and how firefighting changes when dealing with FRPs.
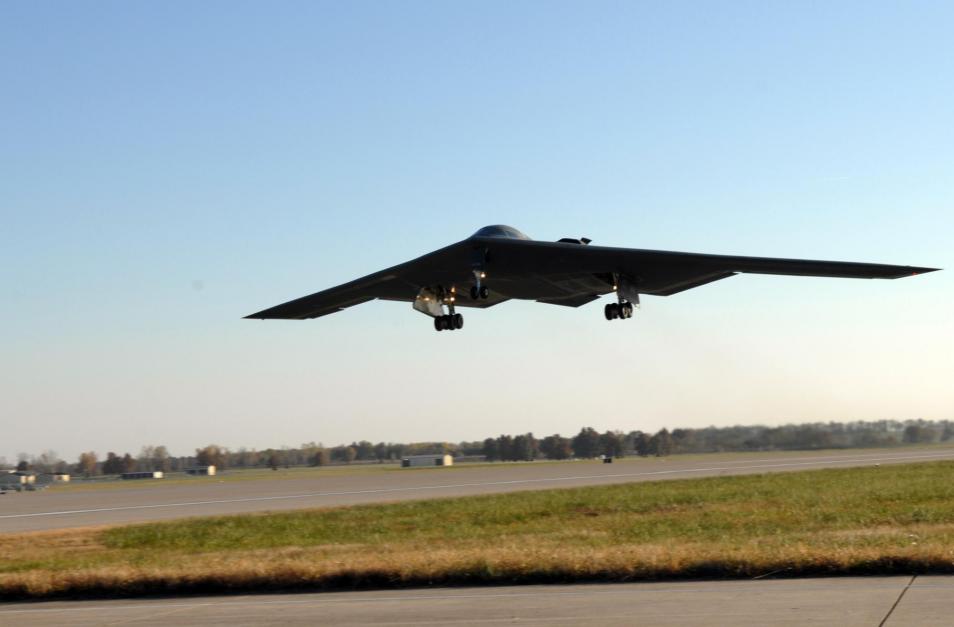
Figure 4: B-2 Bomber Aircraft Performing a “Touch and Go” (Source: U.S. Air Force Airman 1st Class Stephen Linch, http://www.af.mil/News/Photos/igphoto/2000430108/).
SPECIFIC HAZARDS OF COMPOSITES IN FIRE
Mostly carbon-based, FRPs can be considered eventual “fuel” in a fire, unlike ferrous metals. Therefore, just about all the FRP can be involved in the fire and contribute to fire growth. If the FRP matrix material is a “thermoplastic” polymer (it can melt and flow under heat), then once the fire is underway, the material can greatly deform during a fire. This can lead to delamination (increased surface area for accelerated burning) or melt pool formation, which may create an effect like a gasoline-pool fire and rapidly accelerate a fire to ignite other nearby objects or send a compartment to flashover. Flashover means the compartment is completely engulfed in flame (fills all volume of the space) and spills out of the compartment opening, resulting in total fire loss and death to anyone trapped in the compartment. If the FRP matrix material is a thermoset polymer (once it is made, it will not melt again), fire damage can also result in delamination during the fire; however, melt pool formation does not occur. Along with the obvious flame and heat release from a burning FRP (whether thermoplastic or thermoset) and the structural failure of the FRP as it goes past its use temperature, smoke release is often common with these materials, and the smoke can be generated in large amounts. Depending on the chemistry of the matrix polymer in the FRP, the smoke can be black and highly sooty. It can contain other gases, presenting toxicity to crew in the compartment and/or corrosive gases damaging electronics as well as causing breathing issues for the crew. Some high-performance polymers for FRPs can have the right chemistry such that their heat and smoke release and toxic gas emissions are quite low in a fire due to how the polymer in the FRP chars (coverts to thermally stable carbon) rather than burns. While these high-performance polymers are preferred for fire protection, their higher costs limit their use to extreme applications such as engine compartments, mission critical hardware, submarines, and spacecraft. Even with submarines, FRP use is highly limited as fire underwater is a highly undesirable event because any gases from the fire must be scrubbed out until the submarine can surface and get fresh air. Depending upon the mission, this may not be an option until some time after the fire occurs. For spacecraft, the issues are even more severe as there is nowhere to escape from fire in a spacecraft, and the emissions must be scrubbed out and fresh oxygen flushed into the compartment. Close attention must be paid to selecting polymer for FRP in a military application because picking the wrong one may result not just in fire issues, but collateral damage to vehicle electronics and crew.
Close attention must be paid to selecting polymer for FRP in a military application because picking the wrong one may result not just in fire issues, but collateral damage to vehicle electronics and crew.
Another FRP component to consider in a fire is fiber reinforcement. While inorganic fibers in FRPs are not combustible, carbon fibers in military FRPs contribute their own unique hazards to a fire. Specifically, carbon fibers conduct heat—they can drive heat from the fire source deeper into the composite structure, causing the entire composite to heat up. Further, carbon fibers oxidize and release needle-like fragments in fires [9], suggesting further health concerns for crew exposed to smoke from the fire and firefighters and repair crews tending to the fire afterwards. National Fire Protection Association 1971 compliant breathing protection gear is strongly recommended for firefighters involved in fighting FRP fires.
COMPOSITE FIREFIGHTING MEASURES
With the specific hazards mentioned, firefighting measures when dealing with FRPs are somewhat different than those used for putting out traditional fuel-based fires in military scenarios. Typical military firefighting extinguishments include water, foams, CO2, halon, and powders for metal fires. Most aircraft fires with large jet fuel pool fires upon crashing (such as the B-2 crash) utilize foam to smother the fuel pool fire so it extinguishes. For metal-based aircraft, once the fuel pool fire is smothered with foam, the metal rapidly cools and the entire fire is out. This is not the case for FRPs. Once FRPs ignite, the foam will simply put out the fuel pool fire, but the FRP will remain hot and will reignite, which may, in turn, reignite the fuel pool fire. Although foam is needed for dealing with a combination FRP/fuel pool fire, it has almost no effect on the FRP itself. While halon will rapidly snuff out the fire of a FRP, the underlying FRP will remain hot and reignite once the halon gas cloud extinguishes. Therefore, to extinguish a burning FRP, the FRP must be cooled with either CO2 or water. To further complicate the scenario, the water which cools the FRP may interfere with the foam on the fuel pool fire. As a result, careful and mindful firefighting must be conducted. Boeing has released special guidance for dealing with fires of their mostly all-composite airlines, the Boeing 787. They issued instructions to airport fire departments on how to extinguish the FRP and what tools to use to fully extinguish the fire. Since carbon fibers in aircraft FRPs are quite strong, Boeing recommends special fuselage-piercing tools and diamond/carbide blade saws to cut through the fuselage to insert hoses to put out the fire and, where appropriate, remove the structure to get at other parts of the aircraft where fire may have spread [10].
Each FRP in specific military applications will present its own fire threats that may or may not be easily dealt with using existing firefighting equipment on hand. For fire risk scenarios that represent unique military threats (incendiary rounds, high explosives, and napalm), how FRPs will behave can only be speculated in this article. Most likely, the FRP will ignite. Depending on the exact event and how the FRP and military threat interact, as well as the chemistry of the FRP itself, there could be cases where the FRP does not ignite because the FRP did not encounter enough heat to undergo significant decomposition. Based on the intensity of the military threat, the FRP may ignite and contribute to a growing fire, resulting in the loss of the vehicle and/or crew. For more traditional fire risk scenarios, however, FRP should be considered as a fire hazard that requires fire protection and specific guidance on firefighting measures when the FRP ignites.
Each FRP in specific military applications will present its own fire threats that may or may not be easily dealt with using existing firefighting equipment on hand.
COMPOSITE FIRE PROTECTION APPROACHES
Since polymers have been well known to be flammable, there are many solutions available for fire protection of polymers for many different nonmilitary fire risk scenarios. Likewise, these same solutions can be leveraged for FRPs in military applications. However, for the unique military threats just mentioned, some of the fire protection solutions for FRPs may or may not be appropriate. Live-fire testing to verify protection may be needed. For more traditional fire threats (post-crash fuel pool fires, short circuits, and open flame threats), proven fire protection approaches exist.
Active Fire Protection Systems
Active fire protection systems in military vehicles and buildings are one of the most common methods of fire protection. Examples of this include sprinkler systems or other extinguishers that react in a fire. Usually, these systems are heat activated. In some cases, they can be manually activated by personnel inside or outside the compartment where the fire is located. When FRPs are involved in the compartment, active fire protection systems that use water are preferred. Halon-type or CO2–based extinguishers will work as well. However, these gases may only snuff out the fire, not cool the FRP and prevent it from reigniting. If the extinguisher puts out the fire quickly, the FRP may never heat up enough to reignite after the extinguishing agent has dissipated. Foam-based sprinkler systems may not always be appropriate for extinguishing FRP-based fires. It should be noted that for mixed material fires (e.g., FRP aircraft inside a hangar with jet fuel), multiple extinguishing systems may be required to ensure all fire threats are addressed. In cases where the compartment containing FRPs is manned, some extinguishing systems may not be allowed and passive fire protection systems may be required.
Passive Fire Protection Systems
Fire Protection Barriers
Fire protection barriers are among the more common solutions for protecting FRPs. The general concept behind the barriers is to make them out of something noncombustible to provide thermal protection to the underlying FRP, thus preventing it from getting hot enough to decompose and ignite. Typical barriers for FRPs include ceramic fiber blankets and metal plates (Figure 5). Where appropriate, some densified ceramic plates may be included where the ceramic plate also serves as an armor tile. Other barriers include intumescent paints. Upon exposure to fire, these paints produce a carbon-based “foam” which slowly combusts but provides good thermal protection. While barriers are common, their weak link is their connection to the FRP and any gaps that may form in the fire protection barrier. If the barrier falls off or is penetrated, cut, or damaged in any way, then that opening is where the fire can directly interact with the FRP, resulting in fire damage at the exposure site.
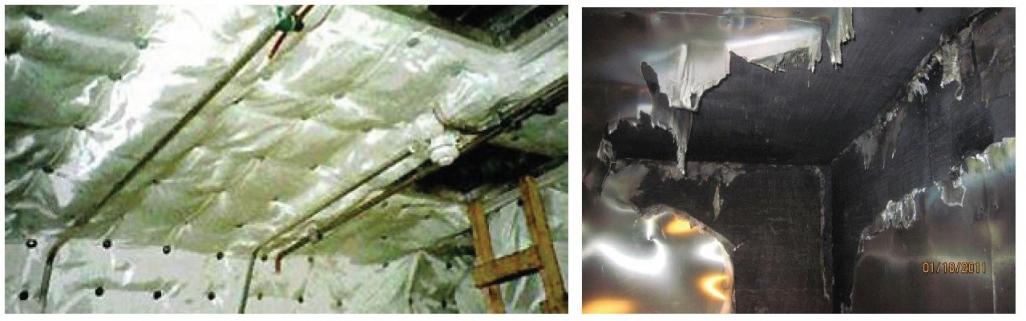
Figure 5: Example of Fire Protection Barriers – Ceramic Fiber Blankets (Left) and Metal Skins Enabling Composites to Pass the Room Corner Test (Right) (Source: Morgan and Toubia [11]).
Newer concepts for fire protection barriers for FRPs include intumescent systems directly bonded to the FRP as a top coat (also known as “gel coat”) to the composite such that the coating cannot be easily damaged/removed from the composite because it is integral to the outer composite layers [12–15]. Another newer concept, although perhaps not as robust to damage, is to create metallized infrared reflective layers reflecting heat away from the sample, thus preventing or slowing ignition of the underlying polymer [16]. While this later concept has not been tested for electromagnetic (EM) interference capabilities, these metallized layers may also provide some unique protection to electronic enclosures or other components sensitive to EM warfare that also need fire protection.
Flame Retardants
Another common solution to providing fire protection to FRPs is to incorporate flame-retardant chemistry directly into the polymer used to make the FRP. There are several flame retardants available for polymers typically used for FRPs, such as epoxies, vinyl esters, and other thermoset polymers. In some cases, the FRPs can be made out of polymers which have inherently low flammability due to their chemical structure. There are numerous review papers on flame-retardant polymers to guide the FRP user on what chemistry to select [17–22]. Ultimately, a balance of properties is required. Specifically, fire safety performance, manufacturability, use temperature (i.e., glass transition temperature), durability, and cost all must be factored into flame-retardant choices for this approach to be successful. Note that flame retardants can be combined with fire protection barriers to give a better balance of properties in the final FRP and provide a more robust fire safety performance as a “defense in depth” should the fire protection barrier be breached.
Structural Reinforcement
Considering the issues mentioned about composites under structural load failing when exposed to heat and fire, sometimes high-temperature metal reinforcement is used to serve as structural support for the FRP in event of a fire. Examples of this include metal superstructure for the fuselage/ hull of a vehicle where the FRPs are connected to the superstructure and do not provide main structural support but rather as secondary vehicle “skins” or compartment walls. When this approach is put in place, fire protection for the FRP and the metal is needed (as is done with metal support structure in buildings today) to prevent the metal from heating up and softening/melting under load.
CONCLUSIONS
FRPs do have an important role in military systems, as they bring good enhancements in properties over metal materials, thus enabling new missions and increased mission range. We should not assume that FRPs and metals can be easily exchanged for one another, as FRPs present their own fire hazards and fire risk scenarios. Further, new firefighting approaches and post-fire hazards with FRPs can be very different than what has been seen with older generation military equipment, where FRPs were only minor components and not typically structural materials. The fire hazards associated with FRPs can be dealt with through understanding the fire threat, paying careful attention to polymer chemistry, and designing the system accordingly. Through a combination of the right polymer chemistry selection as well as active and passive fire protection measures, FRPs can be used in military environments without compromising mission effectiveness or survivability.
References:Â
- Correia, J. R., Y. Bai, and T. Keller. “A Review of Fire Behavior of Pultruded GFRP Structural Profiles for Civil Engineering Applications.” Composite Structures, vol. 127, pp. 267–287, 2015.
- Mouritz, A. P. and A. G. Gibson (editors). Fire Properties of Polymer Composite Materials. Springer-Verlag, The Netherlands: Springer-Verlag, p. 16, 2006.
- Wikipedia. “Alta-Class Minesweeper.” https:// en.wikipedia.org/wiki/Alta-class_minesweeper, accessed 22 May 2018.
- Foxtrot Alpha. “Dear US Navy: The Futuristic X3K Is What Littoral Combat Ships Should Be,” by Tyler Rogoway. https://foxtrotalpha.jalopnik.com/dear-us-navy-the-futuristic-x3k-is-the…, accessed 22 May 2018.
- Wikipedia. “North Sea Boats.” https://en.wikipedia. org/wiki/North_Sea_Boats, accessed 22 May 2018.
- Morgan, A. B. “Flammability of Fiber-Reinforced Polymer Composites for Vehicles.” Fire and Materials 2009 Proceedings, San Francisco, CA, 26–28 January 2009.
- ASTM International. Cone Calorimeter. ASTM E1354, 27 September 2013.
- Wikipedia. “2008 Anderson Air Force Base B-2 Accident.” https://en.wikipedia.org/wiki/2008_Andersen_ Air_Force_Base_B-2_accident, accessed 22 May 2018.
- Eibl, S. “Potential for the Formation of Respirable Fibers in Carbon Fiber Reinforced Plastic Materials After Combustion.” Fire Mater., vol. 41, pp. 808–816, 2017.
- Boeing. “787 Aircraft Rescue & Firefighting Composite Structure April 2013.” http://www.boeing.com/assets/ pdf/commercial/airports/faqs/787_composite_arff_data. pdf, accessed 22 May 2018.
- Morgan, A. B. and E. Toubia. “Cone Calorimeter and Room Corner Fire Testing of Balsa Wood Core / Phenolic Composites Skin Sandwich Panels.” J. Fire Sci., vol. 32, pp. 327–344, 2014.
- Kandola, B. K. and W. Pornwannachai. “Enhancement of Passive Fire Protection Ability of Inorganic Fire Retardants in Vinyl Ester Resin Using Glass Frit Synergists.” J. Fire Sci., vol. 28, pp. 357–381, 2010.
- Kandare, E., A. K. Chukwunonso, and B. K. Kandola. “The Effect of Fire-Retardant Additives and a Surface Insulative Fabric on Fire Performance and Mechanical Property Retention of Polyester Composites.” Fire Mater., vol. 35, pp. 143–155, 2011.
- Kandare, E., C. Chukwudole, and B. K. Kandola. “The Use of Fire-Retardant Intumescent Mats for Fire and Heat Protection of Glass Fibre-Reinforced Polyester Composites: Thermal Barrier Properties.” Fire and Materials, vol. 34, pp. 21–38, 2010.
- Morgan, A. B. and S. Putthanarat. “Use of Inorganic Materials to Enhance Thermal Stability and Flammability Behavior of a Polyimide.” Polym. Degrad. Stab., vol. 96, pp. 23–32, 2011.
- Schartel, B., U. Beck, H. Bahr, A. Hertwig, U. Knoll, and M. Weise. “Sub-micrometre Coatings as an Infrared Mirror: A New Route to Flame Retardancy.” Fire Mater., vol. 36, pp. 671–677, 2012.
- Morgan, A. B. and A. Z. Worku. “Flame Retardants: Overview.” Kirk Othmer Encyclopedia of Chemical Technology, Hoboken, NJ: John Wiley & Sons, 2015.
- Morgan, A. B. and C. A. Wilkie (editors). Non- Halogenated Flame Retardant Handbook. Hoboken, NJ: Scrivener Publishing LLC, 2014.
- Wilkie, C. A. and A. B. Morgan (editors). Fire Retardancy of Polymeric Materials, 2nd edition. Boca Raton, FL: Taylor and Francis, 2010.
- Weil, E. D. “Fire-Protective and Flame-Retardant Coatings – A State-of-the-Art Review.” J. Fire Sci., vol. 29, pp. 259–296, 2011.
- Levchik, S., A. Piotrowski, E. Weil, and Q. Yao. “New Developments in Flame Retardancy of Epoxy Resins.” Polym. Degrad. Stab., vol. 88, pp. 57–62, 2005.
- Levchik, S. V. and E. D. Weil. “Thermal Decomposition, Combustion and Flame-Retardancy of Epoxy Resins – A Review of the Recent Literature.” Polym. Int., vol. 53, pp. 1901–1929, 2004.