INTRODUCTION
Three-dimensional (3-D) printing—or “additive manufacturing,” the preferred production-focused term for industrial-quality 3-D printing—is expected to revolutionize manufacturing processes as the technology moves from prototyping and into production. Moreover, this rapid technology development, combined with the ongoing decrease in cost and increase in popularity, has enabled a wide range of defense applications.
The 3-D-printing revolution brings with it two major advantages: (1) lightweighting, and (2) on-demand parts production for complex systems. For the Warfighter, 3-D lightweighting will impact weapons manufacturing directly. Highly publicized activity by hobbyists and leading-edge manufacturers portends a future that likely includes 3-D-printed guns and ammunition.
Likewise, 3-D printing promises many new opportunities for manufacturing spare parts for complex operational systems. If a part can be generated from materials as needed (and where needed) rather than be stockpiled for
a need that may never arise, complex logistical tails can be greatly shortened or eliminated and field inventory can be reduced to as little as raw materials and design files. Better yet, a 3-D scanner could simplify the process of creating a design to fit a problem, even without a pre-existing design file.
The range of materials available for 3-D-printing applications is also expanding at a rapid pace. These materials now include high-performance polymers, flexible silicones, and heat-tolerant metals and ceramics, along with composites and combinations, such as printed circuit boards.
Not surprisingly, the significant advantages and opportunities in 3-D printing for military application also bring considerable safety and security challenges/risks (including the exploitation of these technologies by real and potential adversaries). Thus, the U.S. defense community must stay aware of, and engaged in, technological developments across the advanced manufacturing industry.
HYPE AND REALITY
Much attention has been devoted recently to the 3-D printing of weapons. In fact, it has been feasible to 3-D-print a gun for several years now. For example, Cody Wilson gained notoriety with the printing of the plastic Liberator in 2013 [1]. Wilson’s accomplishment was in some ways a stunt focused on the legal aspects of the effort as much as on its technical achievability.
The 3-D printing of AR-15 components was successfully demonstrated that same year by Michigan-based Sintercore, which later announced the availability of a 3-D-printed magazine extension for the Glock 43 [2]. Manufacturing efforts such as these continue on AR-15’s and other weapons, as well as a wide range of related personal accessories (such as clips, brackets, and carriers), by various hobbyists and others.
An arguably more significant achievement, at least from a technical standpoint, was the metal Reason gun created in 2014 by Solid Concepts. The Reason was a 3-D-printed 10-mm Auto 1911 pistol said to cost $11,000 [3, 4]. More recently, the Army succeeded in printing all the parts (except the springs and fasteners) of a grenade launcher named R.A.M.B.O. (which stands for Rapid Additively Manufactured Ballistics Ordnance) [5]. Billed as functional, accurate, and cost-effective, R.A.M.B.O. (shown in Figures 1 and 2) represents another significant step forward in the 3-D printing of weapons.
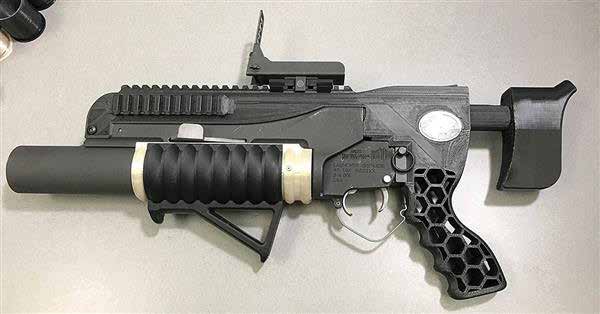
Figure 1: The Army’s R.A.M.B.O. Grenade Launcher (Credit: U.S. Army ARDEC, Source: http://asc.army. mil/web/news-alt-amj17-rambos-premiere/).
It must be remembered, of course, that real dangers to personnel safety can and do exist whenever a weapon (especially a plastic weapon) is manufactured and used. Not the least of these dangers are the violent physical and chemical reactions associated with the functioning of firearms. The high explosive pressures resulting from igniting propellant inside a gun barrel can cause catastrophic failures to a weapon (and potentially lethal injury to a user) if the weapon is not manufactured with the proper material strengths, engineering tolerances, and quality controls.
PRIMARY ADVANTAGES OF 3-D PRINTING
As noted, one of the major advantages of 3-D printing is lightweighting. Additively manufactured parts can be made of lighter materials, and high-performance polymers can sometimes substitute for metal, especially when reinforced by carbon fiber or Kevlar. And even if traditional materials are used, the geometry of 3-D printing is seldom a solid block of material. Open weave areas, honeycomb designs, and even completely redesigned shapes can be optimized within the digital design files to create strong but much lighter parts.
Understandably, this lightweighting advantage is particularly attractive in flight and transportation because it lessens fuel use and leaves more room for cargo, whether in an aircraft, truck, or drone. For weapons, lightweighting can also enhance portability. And even if the actual weapon is not redesigned, 3-D printing can bring weight advantages to clips, brackets, carriers, and other accessories. In addition, drones and microdrones provide considerable opportunity, as every gram saved in drone weight can be used for payload.
The other clear advantage of 3-D printing is the ability to generate objects (including relatively complex objects) in small batches and close to where they are needed. This aspect not only addresses the need in the field to supply on-demand parts, but it has broader implications for the supply chain as well. In short, if one can create a part on demand, one does not need to maintain, supply, or protect a warehouse of parts in the field.
If one can create a part on demand, one does not need to maintain, supply, or protect a warehouse of parts in the field.
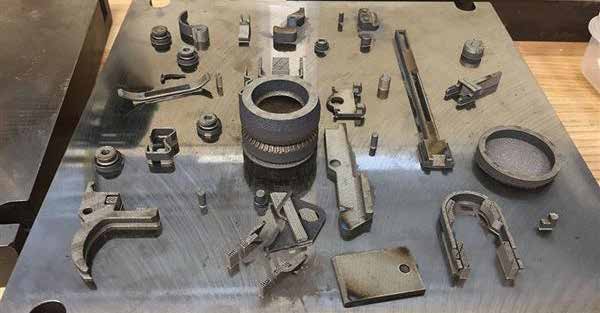
Figure 2: R.A.M.B.O.’s 3-D-Printed Parts (Minus the Receiver and Barrel) (Credit: U.S. Army ARDEC, Source: http://asc.army.mil/web/news-alt-amj17-rambos-premiere/).
3-D PRINTING AND THE SUPPLY CHAIN
The supply chain model of the future is expected to incorporate 3-D printing. The model relies on stockpiling material and then creating the needed part on demand. In 2014, NASA demonstrated an excellent example of applying this model in space. Astronauts on the International Space Station, who had a 3-D printer (modified to overcome the gravity-based layering model), needed a ratchet wrench to fix a particular problem. As the closest hardware store was, to say the least, not easily accessible, they requested software with the given dimensional measurements, got everything validated and approved, printed the wrench, and successfully fixed their problem [6].
If 3-D printing and the supply chain model can be successfully applied in space, the possibilities for what might be done on Earth are virtually endless. As for space, 3-D printing is part of the shelter concept for a possible Mars mission, including a plan to use a 3-D printer to potentially create objects, including buildings, using Mars soil. Likewise, in a military context, Special Forces or other forces deployed in remote areas around the world could have the ability to quickly create whatever equipment they need whenever and wherever they need it.
Furthermore, incorporating artificial intelligence into the process could provide even greater opportunities and applications for 3-D printing. With a 3-D scanner, it is possible to scan a problem part (e.g., a cracked bracket) as well as a baseline part (e.g., an intact bracket) for comparison. Intelligent software could then potentially “propose” both a geometry and a material fix (e.g., “Heat-resistant to 60 °C, light-resistant, slightly flexible, carbon fiber reinforcement advisable: Use material 96N.”).
Special Forces or other forces deployed in remote areas around the world could have the ability to quickly create whatever equipment they need whenever and wherever they need it.
It should be noted here, however, that the “print-anywhere” model can be a little misleading. There are many printer versions that are optimized for many different materials and tasks. It is thus likely that many types of printers will be needed to replace our supply depots. The supply chain will also still include handoffs, because not every need will be fulfilled by a single printer one can monitor personally. Additionally, that supply chain, with its handoffs, will include all the usual vulnerabilities to fraud and sabotage, further complicated by the counterfeiters’ ability to produce excellent copies, potentially with hidden flaws. Digital files and models must thus be protected via cybersecurity, coupled with an approach for cyber-physical security.
Likewise, as reverse engineering of weapons increasingly becomes a matter of 3-D scanning and replication, counterfeiters and adversaries will increasingly be able to make their own versions, thus magnifying the importance of validation. Thus, the easier it is for rogue players to insert fakes into the supply chain, the more important it is to enshrine authentication into the process.
AUTHENTICATION PROTECTIONS FOR 3-D PRINTING
Other types of authentication controls are appropriate in the context of weapons. It may be necessary to incorporate “do-not-copy” provisions into scanners and printers, limiting replication in the same way that color copiers in the United States thwart copying of currency. It may also make sense to incorporate authentication and tracking into 3-D-printed weapons and ammunition.
Current protection options in the 3-D printing arena fall into two general categories. First, cybersecurity protections manage the use and reuse of the digital file. Part of the protection scheme incorporates digital rights management, dealing with questions such as “Does a particular individual have the right to use this file, and if so, are there restrictions on how many times he/she can use it (and with which printers and materials)?” Other cybersecurity concerns include access to the printer’s industrial controls, dealing with questions such as “Is the printer protected from sabotage to its cooling systems, laser safety, and print quality controls?”
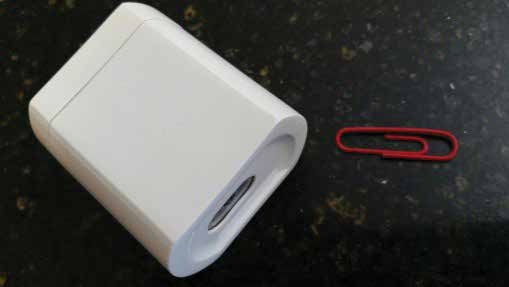
Figure 3: Example of a COTS Pocket-Sized Spectrometer for Authentication (Source: InfraTrac).
The second area of protection addresses the printed object. Conventionally, objects are protected with some sort of covert marking (on the product or label), conveying authenticity. Such covert indicators, however, are often easy to spoof. For example, if a product conveys authenticity with a hologram, it is not that difficult for a counterfeiter/adversary to put a hologram on the fake product as well. In fact, the advent of 3-D scanning and replication can further exacerbate the problem. Whatever the mark on the product, a 3-D scanner can see it and make it appear, as a kind of hijacked mark of authenticity, on the copy.
For this reason, chemical tagging schemes should be preferred over visual marks. Options include quantum dots, which may eventually emerge as a solution but currently have scale-up and supply chain issues (not to mention toxicity concerns regarding cadmium and lead). DNA taggants have also been employed in the supply chain, but full verification requires sequencing (which is not yet field-friendly) and most 3-D printing processes involve temperatures that are too high for DNA to be usable.
Chemical fingerprinting with spectroscopic taggants, hidden in an invisible layer within the print, has been called the most promising technique for authentication protection [7]. This technique, which uses chemical taggants controlled by the print process, could be likened to one hiding a spot of peanut butter and jelly in the “sandwich” of the many 3-D print layers [8]. The chemical “fingerprint” can then be validated quickly and nondestructively with a commercial off-the-shelf (COTS) light-based hand-held spectrometer (such as the one shown in Figure 3).
CONCLUSION
Overall, emerging 3-D printing/additive manufacturing technologies are poised to transform standard manufacturing and supply chain practices, and weapons and the DoD community are certain to be part of this transformation. As mentioned, the advantages this transformation promises include lightweighting products and on-demand production capabilities. But with these advantages come challenges as well—including critical safety and security issues — that military planners and developers will have to address as they move forward and find new ideas and applications for this exciting emerging technology.