A NEW VISION
The last decade has seen a resurgence of NASA’s bold visions, from returning humans to the moon after a 50-year hiatus to colonizing Mars. President George W. Bush addressed NASA and the nation on 14 January 2004 to present this vision as the Renewed Spirit of Discovery [1, 2, 3]: Inspired by all that has come before, and guided by clear objectives, today we set a new course for America’s space program. We will give NASA a new focus and vision for future exploration. We will build new ships to carry man forward into the universe, to gain a new foothold on the moon, and to prepare for new journeys to worlds beyond our own. In his address, President Bush established three goals to accomplish the new objectives outlined for NASA: (1) completing the International Space Station (ISS) by 2010, (2) developing and testing a new spacecraft (the Crew Exploration Vehicle) for initially ferrying astronauts to the ISS and ultimately carrying humans beyond Earth orbit to other worlds, and (3) return to the moon by 2020 as a launching point for missions beyond. A key challenge to achieving these objectives that the president mentioned in his address was the expense of lifting heavy cargo into Earth orbit, limiting our ability to fund a multitude of desirable missions. As he pointed out, “Lifting heavy spacecraft and fuel out of the Earth’s gravity is expensive.”
LEAVING LOW EARTH ORBIT TO COMMERCIAL VENTURES
The president’s vision for NASA would be accompanied by a number of other decisions and technology solutions needed to make them viable. NASA would eventually abandon exploring opportunities in Low Earth Orbit (LEO), where the ISS is located (see Figure 1), while encouraging future exploitation by other entities, such as educational, private, nonprofit, and commercial organizations [4]. For example, promoting competition for developing small satellites, such as CubeSat [5], has advanced satellite technologies for low-cost use of space. Currently, small satellites for commercialization of space are relatively inexpensive to fabricate (<$10,000). However, the cost to lift them to LEO, even in bundles, remains comparatively high per kilogram mass (see Table 1). Furthermore, commercial launches of small payloads have not expanded greatly over the past decade due to cost, scheduling uncertainties, risk of failure, and undesirable orbit placement [4, 6].
Robert Heinlein, a noted science-fiction writer, made a profound and illustrative comment regarding space travel [7]. “Once you get to Earth orbit,” he said, “you’re halfway to anywhere in the solar system.”
His meaning reflects the need for expending an enormous amount of energy to reach that point, while going anywhere else beyond requires a negligible amount. This comment is also a reflection of the cost of space travel, where launch costs can consume a large portion of the mission costs. (For more information on space propulsion, see our article entitled “Space Travel Aided by Plasma Thrusters: Past, Present, and Future” in the spring 2017 DSIAC Journal [8].)
Cost-effective access to space for future commercial and government use must rely heavily on reducing the price for launching cargo beyond Earth’s gravity to desired orbit destinations and provide ample scheduling opportunities. An abundance of potential benefits will exist when launch costs are lowered and LEO is made more accessible. More frequent launches, more competition for commercialization, more opportunities for small businesses, more opportunities for research in low-gravity environments, and expansion of human flight beyond Earth’s gravity are just a few.

Figure 1: Earth’s Near Orbits and Atmospheres (NOTE: Distances Not to Scale).

Table 1: Current Orbital Launch Vehicles in the United States [12]
LAUNCHER SIZE AND COST
Since the 1950s and the start of the space race, launch vehicles in the United States and other countries have grown immensely, not only in terms of size, but in cost. Figure 2 shows the progression in size for several launch vehicles in NASA’s Launch Services Program [9]. As shown in Table 1, overall costs per launch for the Delta IV vehicle have reached as high as $400 million. NASA’s retired Saturn V rocket (not shown), one of the largest to fly, was 111 m (363 ft) tall, weighed 2.8 million kg (6.2 million lbs) and carried around 118,000 kg (130 tons) of cargo. Costs reached about $1.2 billion per launch [10]. Its last mission launched Skylab into Earth orbit in 1973 [11].
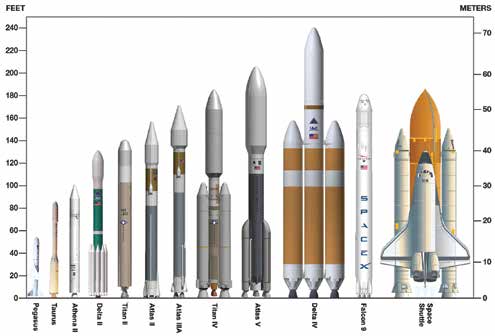
Figure 2: U.S. Launch Vehicle Comparison [9]. (NOTE: Space Shuttle Shown for Size [Height] Comparison Only).
NASA continues the trend to larger vehicles with its proposed newest member in the heavy-lift launch family, the Space Launch System (SLS) Block 2 vehicle. This vehicle is destined to take humans beyond Earth orbit. At roughly 112 m (365 ft) tall, it will weigh nearly 3 million kg (6.5 million lbs) and is expected to carry 130,000 kg (268,000 lbs) of cargo into orbit using three stages. Five-segment solid rocket boosters (SRB), more powerful than those used on the Space Shuttle, will help propel the vehicle out of Earth’s low atmosphere [13, 14]. Early unofficial estimated costs per launch were $500 million to $1 billion, with only two or three launches per year to LEO with this expendable vehicle [15, 16].
NASA and commercial companies have recognized that launch costs vary considerably depending on cargo, mission, facilities, and supplier. Past experience has shown that launch costs can reach $34,000/kg of cargo [4, 17] for primarily expendable vehicles. However, more recent launches by Space Exploration Technology (SpaceX) have demonstrated launch costs less than $5,000/kg [4]. Unfortunately, these costs still prohibit some small start-up venture companies from participating in the small- to mediumsized commercial satellite market. Launch suppliers will need to provide costs in the neighborhood of $2,000/kg of cargo [18], while assuring ample availability to flight schedules and destinations (precise orbits) to cultivate a more competitive market. SpaceX currently claims entry to this level of pricing to LEO based on its Falcon Heavy rocket, which is a fully expendable vehicle [19]. The long-term goal is to bring LEO launch costs to no more than the price of a commercial airline fare.
An abundance of potential benefits will exist when launch costs are lowered and LEO is made more accessible.
REUSABLE VEHICLES, A KEY TO REDUCING LAUNCH COSTS
At present, several initiatives have sought to reduce launch costs based on reusable vehicles. Most noteworthy were the recent achievements by SpaceX. With support from NASA over the past several years, SpaceX has completed many successful orbital launches with its Falcon 9 rocket, including resupply missions to the ISS and the demonstration of a recoverable and reusable first-stage rocket in March 2017 [20].
Blue Origin is another company that has taken part in development and demonstration of reusable launch vehicles. Its suborbital rocket employs the company’s BE-3 engine using liquid hydrogen (LIH) and liquid oxygen (LOX). Designed to travel nearly 110 km above the earth (Karman line), several successful tests have been demonstrated with their New Glenn reusable single-stage booster rocket [21] (depicted in Figure 3). At this time, Blue Origin has the ability to launch small 50-lb payloads to the Karman line, with up to 4 min of weightlessness for experimental tests. Eventually, two- and three-stage vehicles powered by Blue Origin’s BE-4 engines will launch a capsule with up to six astronauts into LEO and then return the reusable first stage to Earth. The BE-4 engines will burn liquid natural gas (LNG) and LOX and have 5 times more thrust than their BE-3 counterparts. Launch costs are not publicly known at this time, but Blue Origin advertises human flights to the edge of space by 2020 as one of its near-term commercial ventures.
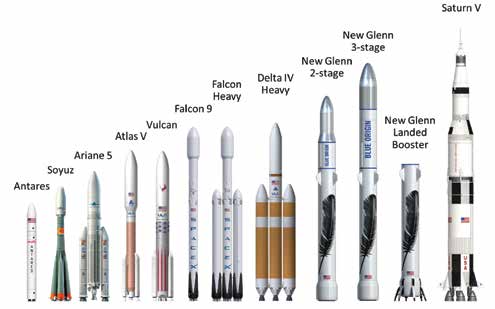
Figure 3: Size Comparison of New and Old Launch Vehicles.
Figure 3 compares the design and size of these new and old launch vehicles. Table 2 describes future launch vehicles for accessing LEO as provided by the Federal Aviation Administration Annual Compendium [12]. Vehicles that employ expendable and reusable stages are indicated, along with estimated launch price/kilogram of cargo, with reusable vehicles generally providing lower costs. Both SpaceX and Blue Origin advertise reusable first stage rockets from multistage vehicles, with SpaceX offering launch costs below $5,000/kg. However, the United Launch Alliance (ULA) with its Vulcan vehicle set to launch in 2019 may prove to be competitive even without reusable hardware.
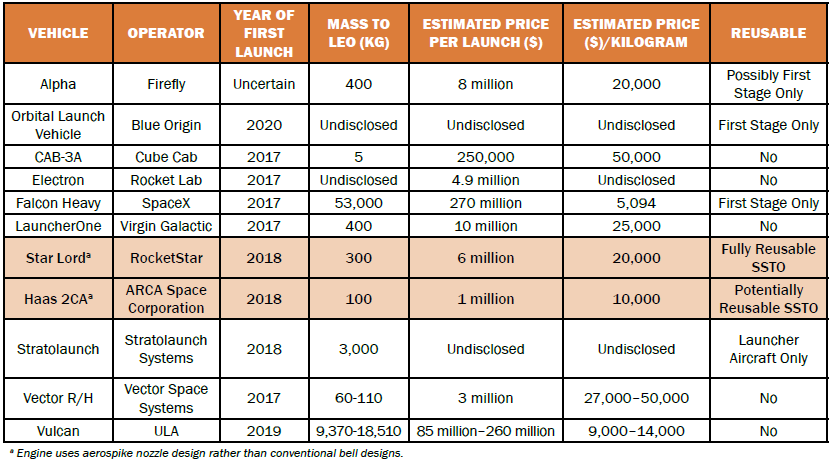
Table 2: Future Orbital Launch Vehicles in the United States [12]
Companies such as those shown in Tables 1 and 2 typically offer secondary (piggy-back) launch services for small satellites to maintain low costs for small commercial ventures. However, these types of launches using heavylift vehicles limit orbit placement and scheduling opportunities because they are driven by primary customers who have specific requirements (and who supply the majority of funding). Pegasus XL launched by Orbital ATK from a reusable L-1011 airliner offers single-payload services and specific orbit placement, but at a high price of $89,000/km, as shown in Table 1. The L-1011 launcher is considered reusable hardware, replacing an expendable firststage rocket.
The successes and future prospects described previously for Earthbased launch vehicles have certainly opened new opportunities for the commercial use of LEO, especially with the demonstration of reusable firststage rockets. However, further cost reductions may only be afforded by using a future fleet of fully reusable vehicles that will have a life expectancy (reuse capability) rivaling today’s commercial and defense aircraft, some of which have flown for more than 50 years. Keys to unlocking the development of fully reusable vehicles may lie in two areas of vehicle technology: (1) reuse of all stages from multi-stage rockets, and (2) reintroduction and development of reusable single-stage-to-orbit (SSTO) vehicles, which can eliminate the need for multiple stages. Imagine a fleet of recoverable vehicles that can be delivered in 1 to 2 decades and have a 50-year life span. Conceivably, this fleet could provide flexible and multiple launches every year during their life time and offer precise orbit placement of cargo and human travelers at the price of a commercial airline ticket.
THE AEROSPIKE ENGINE
In the 1960s, NASA described development of a vehicle using an aerospike rocket nozzle concept that could provide a fully reusable SSTO vertical-launch rocket [22, 23]. These nozzles allow for optimum operation of rockets at all altitudes, rather than relying on less efficient multiple stages that are designed to operate in specific altitude (pressure) ranges. Figure 4 compares the aerospike nozzle concept to a conventional bell nozzle. When used in linear or annular arrangements, they may also provide steering capability by throttling fuel flow through each nozzle, thereby eliminating attitude control systems. Mechanical thrust vector control (TVC) can also be accommodated on an aerospike engine array.
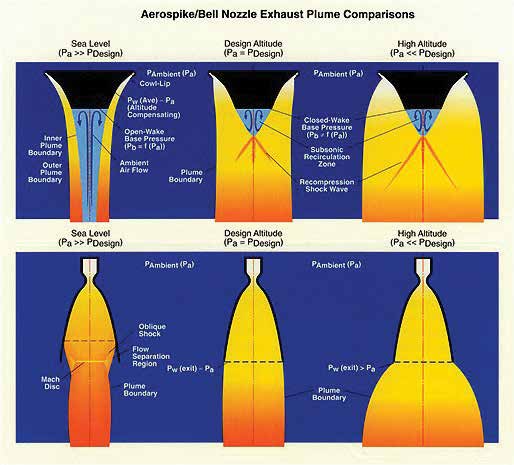
Figure 4: Aerospike Nozzle Concept Compared to a Conventional Bell Nozzle.
How Aerospike Nozzles Work
As shown in Figure 5, aerospike engines are fundamentally altitude (pressure)- compensating designs and bear a similarity in function to internal pressurecompensating pintle (controllable) nozzles. The unique aerospike design can be visualized as a self-adjusting inside-out pintle nozzle without moving parts. The surrounding atmosphere acts as the pressure-compensating boundary (atmospheric bell). Liquid or gaseous fuel is pumped through injectors at the forward end (entrance) of the nozzle, ignited, and then burned to provide thrust. Rather than constrict the exhaust gases inside a conventional bell nozzle, the aerospike nozzle directs the gases along the exterior of the “spike.”
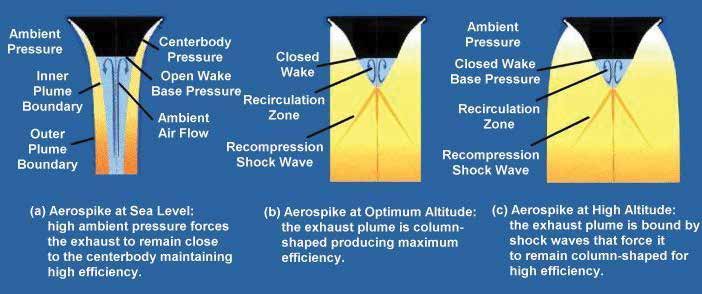
Figure 5: Operation of Aerospike Nozzles (Source: Aerospaceweb.org).
One of the advantages these nozzles have over conventional nozzles is that they typically use 25–30% less fuel at low altitudes, where a large fraction of the on-board rocket fuel is consumed to generate initial thrust for accelerating heavy vehicles through the lower atmosphere. Beyond having the weight and cost advantage of carrying and consuming less fuel than conventional nozzles, aerospike nozzles can also be conveniently arranged in multiple linear or annular configurations, be throttled individually for steering, and be easily adapted for mechanical TVC. Most importantly, aerospike nozzles provide an excellent opportunity for advancing fully reusable SSTO space launch vehicles by eliminating multiple expendable stages. Aerospike nozzles can also employ materials that have already proven useful and critical for conventional bell nozzles, thereby minimizing the need for costly development and demonstration of new technologies and materials. Furthermore, the use of three-dimensional (3D) (or additive) manufacturing can offer opportunities in reducing manufacturing costs and weight in aerospike nozzle geometries and ancillary components.
Early Aerospike Vehicle Concepts
Blending space and flight technologies, the aerospike nozzle engine was first destined for use on NASA’s X-33 vehicle and Reusable Launch Vehicle (RLV) space planes, shown in Figure 6. A 20%-scaled-down version of the X-33 reusable space plane with nine linear aerospike nozzles and its ancillary hardware were first tested for aerodynamics and component integrity atop an SR-71 aircraft [24]. Many tests for evaluating safety using inert gas flowing through the craft’s engines (cold flow tests) and many live-fire ground tests were conducted. However, no live solo launch or flight tests were performed due to LOX leaks in the fuel system. Because enough live-fire data were gathered from ground tests, launch and live solo flight tests were discontinued and the project was abandoned. Interestingly, the RLV space plane was projected to lower the cost of satellite launches to 1/10th that of the Space Shuttle by adapting aircraft-type landing, inspection, refueling, and reuse.
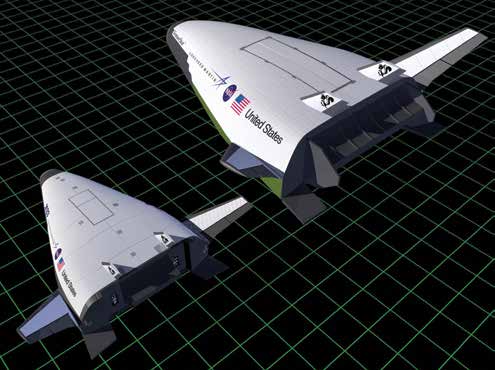
Figure 6: X-33 and RLV Concept Drawings With Multiple Linear Aerospike Engines (Source: NASA).
Flight Successes With Aerospike Nozzles
In 2004, approximately 40 years after its conceptualization, a solid-fueled toroidal aerospike engine was first flown jointly by NASA, the U.S. Air Force, and Blacksky Corporation [25]. Figure 7 shows Blacksky’s aerospike nozzle, which allowed its rocket to exceed Mach 1.5 and achieve altitudes above 8 km (over 26,000 ft). Patrick Lemieux from California Polytechnic State University later designed and successfully tested an aerospike engine using a hybrid rocket motor with nitrous oxide and a solid fuel. The engine was tested repeatedly several times using cooling of ablative materials to reduce erosion, thereby demonstrating reusability even in highly corrosive and thermal environments [26]. Firefly Space Systems succeeded in demonstrating a first-stage aerospike engine using LOX and RP-1 fuel in a ground test of its Alpha launcher [27]. Although never flown or fully demonstrated, the Firefly Alpha launcher planned to use 12 aerospike nozzles in a circular array.
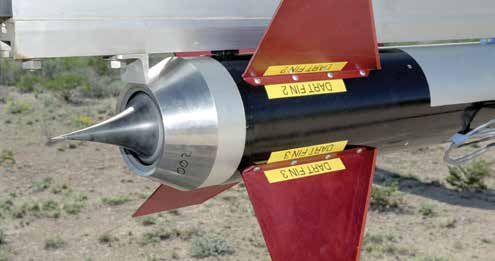
Figure 7: Close-up Photograph of Blacksky’s Aerospike Nozzle Flown in 2004 (Source: NASA)
THE RACE TO THE KARMAN LINE AND THEN ON TO LOW EARTH ORBIT
As the need for low-cost launch technology continues, corporations are revisiting the use of aerospike engines for launching payloads to LEO with the intent of providing fully reusable launch vehicles and low-cost access to space. RocketStar recently cosponsored a project at Stony Brook University to assess the feasibility and document the history of aerospike engines [28]. The report from this effort discusses improved performance with aerospikes compared to conventional bell nozzles and outlines previous tests with various aerospike designs (toroidal, truncated, and others).
As part of a progressive plan to demonstrate the feasibility of aerospike nozzles prior to LEO launches, RocketStar recently conducted a ground test of a nearly 2-m-long sounding rocket designed to reach an approximate 3-km altitude. The rocket also used a 3D-printed aerospike engine. This test showed promise for solid booster technology as the aerospike nozzle produced an average performance improvement of 22.4% over a traditional bell nozzle during low-power tests and static firing. The rocket ultimately reached more than 3 km and 0.88 speed of sound [29].
Attempting to win the race to the Karman line prior to the end of 2017, RocketStar’s next step will be to launch a 7.62-m aerospike suborbital rocket to the edge of space as a prerequisite to its first LEO launch. The launch will be used to evaluate the novel toroidal nozzle geometry and carbon fiber composite fuel tank and fins.
Following the test to reach the Karman line, RocketStar is planning to launch a fully reusable aerospike vehicle to LEO as early as the first quarter of 2018. The company’s orbital launcher, Star Lord (Figure 8), will also rely heavily on 3D printing technology to minimize manufacturing costs. Injectors, most of the flight motor, and some of the main fuselage parts will use additive manufacturing. Star Lord is designed to be a completely reusable SSTO rocket and will be recovered from its first launch in early 2018. Similar in size to an Orbital ATK Minotaur rocket, Star Lord will take multiple CubeSat satellites, or one large satellite, into LEO and deploy them before the rocket returns to Earth, demonstrating that an SSTO rocket can be recovered, validated as flight worthy, and then flown again. RocketStar’s ultimate goal is to achieve routine lowcost small satellite launches with a fleet of reusable rockets having a life span similar to today’s commercial aircraft [30].
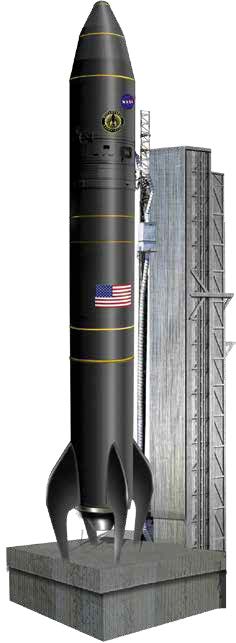
Figure 8: RocketStar Star Lord With Truncated Aerospike Nozzle.
Currently, RocketStar projects a cost of approximately $20,000/kg for small satellite launches starting in 2018 (see Table 2), along with potentially convenient schedules and destinations. Plans for achieving consumer accessible costs, with figures closer to $6,000/kg over the next few years, are in place and will rely on successful ground and flight tests as commercial vehicles mature. In addition, the company fully expects the cargo costs per kilogram to shrink to a few hundred dollars within 10 years and is embracing the concept of building a fleet of fully reusable space launch vehicles to support commercialization of LEO for many years to come.
ARCA Space Corporation has also announced the development of an SSTO vehicle, the Haas 2CA (shown in Figure 9), with flight testing expected in 2018. This vehicle will burn hydrogen peroxide and RP-1 fuel for propelling a 100-kg payload within a 24-hr notice. With a projected launch cost of approximately $1 million to LEO for small payloads [31], the price translates to about $10,000/kg of cargo. ARCA has not disclosed plans to recover the Haas 2CA SSTO vehicle following the first LEO launch.
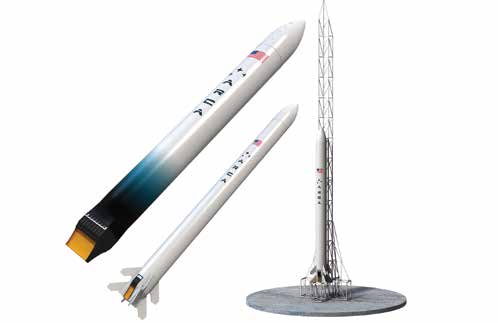
Figure 9: ARCA Haas 2CA and Demonstrator 3 Vehicles [32].
Also as a prerequisite to a future LEO launch, a flight of the ARCA Demonstrator 3 suborbital rocket with a linear aerospike design, using only clean-burning low-flame-temperature hydrogen peroxide, is planned before the end of 2017 [32]. Competing in the race to reach the edge of space, this flight will validate ARCA’s aerospike engine design and the use of a composite fiber fuel tank prior to the critical first launch of the Haas 2CA vehicle for achieving LEO.
CONCLUSIONS
The past half-century in the space industry has witnessed significant achievements in launch vehicle size and power for placing increasingly heavier payloads into LEO and beyond. However, the potential for further exploitation and commercialization of LEO has suffered primarily due to high launch costs. Currently, the space launch industry is at a turning point, where new achievements have been witnessed for reducing launch costs, presenting opportunities for low-cost use and commercialization of LEO and offering human space travel to the private sector. Over the past decade, commercial companies such as SpaceX have sought, and recently demonstrated, the feasibility of reusing rocket hardware. This first step, which takes advantage of reusing expensive first stage rockets, has introduced a new era in the space industry. This trend for reducing costs is destined to continue by demonstration of the reuse of additional stages, along with cargo and crew vehicles.
Furthermore, success in reusing rockets is awakening a renewed interest in aerospike nozzle technology that offers the potential for a completely reusable SSTO vehicle. Initially investigated by NASA for space plane concepts, aerospike nozzles offer a path to eliminate expensive multi-stage rockets by using an SSTO vehicle. Coupled with the ability to recover and reuse rocket hardware, aerospike nozzle technology also has the potential to reduce overall rocket size and weight through more efficient use of on-board fuel. With such achievements on the horizon, accessing and using LEO for commercial development and educational research is attainable at reasonable costs. Before the end of this decade (or soon after), cargo and humans may begin to travel routinely to a low-gravity environment for no more than the cost of a commercial airline fare as the status quo of space travel is altered forever.
References:
- Office of the Press Secretary. “President Bush Announces New Vision for Space Exploration Program.” Press release, NASA Headquarters, Washington, DC, 14 January 2004.
- NASA. “The Vision for Space Exploration.” NASA Memorandum NP-2004-01-334-HQ, February 2004.
- Wall, Mike. “NASA Eyeing Mini Space Station in Lunar Orbit as Stepping-Stone to Mars.” Space.com, http://www.space.com/36270-nasa-deep-space-gateway-moonorbit.html, accessed 30 March 2017.
- Besha, P., and A. MacDonald. “Economic Development of Low Earth Orbit.” NASA Monograph NP-2016-03- 2140-HQ, published 2015.
- NASA. “CubeSats.” https://www.nasa.gov/mission_ pages/cubesats/index.html, accessed 15 June 2017.
- Federal Aviation Administration. “Annual Compendium of Commercial Space Transportation: 2016.” January 2016.
- Quote Wise. http://www.quote-wise.com, accessed April 2017.
- DeFusco, Albert, Christopher Craddock, and Wesley Faler. “Space Travel Aided by Plasma Thrusters: Past, Present, and Future.” DSIAC Journal, vol. 4, no. 2, spring 2017.
- NASA. “NASA’s Launch Services Program.” NASA Fact Sheet FS-2012-03-059-KSC, 15 March 2012.
- Williams, Matt. “Here’s How SpaceX’s Falcon Heavy Rocket Compares to the Apollo Moon Rocket.” Business Insider, http://www.businessinsider.com/spacex-falconheavy-vs-apollo-saturn-v-roc…, accessed 26 July 2017.
- NASA. “Rocket Park.” https://www.nasa.gov/ centers/johnson/rocketpark/saturn_v.html, accessed April 2017.
- Federal Aviation Administration. “The Annual Compendium of Commercial Space Transportation: 2017.” January 2017.
- NASA. “Space Launch System at a Glance.” NASA Publication NP-2015-09-83-MSFC, 20 October 2015.
- NASA. “Space Launch System: Building America’s New Rocket for Deep Space Exploration.” NASA Fact Sheet FS-2016-02-04-MSFC, October 2015.
- Wall, Mike. “NASA’s Huge New Rocket May Cost $500 Million Per Launch.” Space.com, https://www. space.com/17556-giant-nasa-rocket-space-launch-cost. html, accessed 19 July 2017.
- Strickland, John. “Revisiting SLS/Orion Launch Costs.” The Space Review, http://www.thespacereview. com/article/2330/1, accessed 19 July 2017.
- NASA. “Space Launch Initiative, Technology Summary, Propulsion.” NASA Fact Sheet FS-2001-00-00- MSFC, Pub 8-1320, 2001.
- NASA. “Space Launch Initiative, Technology Summary, NASA Unique Systems.” NASA Fact Sheet FS-2001- 00-00-MSFC, Pub 8-1319, 2001.
- SpaceX. “Capabilities & Services.” http://www. spacex.com/about/capabilities, accessed May 2017.
- SpaceX. https://www.youtube.com/watch?v=xsZ SXav4wI8&feature=youtu.be, “World’s First Reflight of an Orbital Class Rocket | SES-10 Hosted Webcast.” accessed 4 July 2017.
- Blue Origin. “New Shepard In-Flight Escape Test.” https://www.blueorigin.com/news, accessed 15 May 2017.
- Corda, S., B. A. Neal, T. R. Moes, T. H. Cox, R. C. Monaghan, L. S. Voelker, G. P. Corpening, R. R. Larson, and B. G. Powers. “Flight Testing the Linear Aerospike SR-71 Experiment (LASRE).” NASA Technical Memorandum TM-1998-206567, Presented at 30th Anniversary Symposium of the Society of Flight Test Engineers, Reno, NV, 15–17 September 1998.
- Hicks, John W., and Gary Trippensee. “NASA Hypersonic X-Plane Flight Development of Technologies and Capabilities for the 21st Century Access to Space.” AGARD Future Aerospace Technology in Service to the Alliance, Paris, France, 14–18 April 1997.
- NASA. “Past Projects: Lineal Aerospike SR-71 Experiment (LASRE).” https://www.nasa.gov/centers/ dryden/history/pastprojects/SR71/Lasre/index.html, accessed 31 May 2017.
- Spaceflight Now. “First Aerospike Engine Flight Test Successful.” https://spaceflightnow.com/news/ n0404/19aerospike/, accessed 1 June 2017.
- Lemieux, P. “Development of a Reusable Aerospike Nozzle for Hybrid Rocket Motors.” AIAA 2009-3720, Presented at the 39th AIAA Fluid Dynamics Conference, San Antonio, TX, 22–25 June 2009.
- Wall, Mike. “New Firefly Rocket Engine Passes Big Test, Will Launch Small Satellites.” Space.com, http://www.space.com/30508-firefly-rocket-engine-test-photo.html, accessed 1 June 2017.
- Subrat, J. “Preliminary Technical Feasibility and Literature Review of Aerospike Engines.” Phase I Final Report, Stony Brook University, 9 December 2014.
- Wenz, John. “RocketStar Wants to Make Going to Space a One-Step Process.” Popular Mechanics, http:// www.popularmechanics.com/space/rockets/a18245/ rocketstar-space-single-stage-to-orbit/, accessed 1 June 2017.
- Yahoo Finance. “RocketStar Partners With TriSept Corporation for Small Satellite Launches.” https://finance.yahoo.com/news/rocketstar-partners-trisept-corporation-s…, accessed 1 June 1, 2017.
- Szondy, David. “From Earth to Orbit Using a SingleStage Rocket. New Atlas, http://newatlas.com/singlestage-rocket/48710/?li_source=LI&li_medium=def…, accessed 1 June 2017.
- ARCA Space Corporation. “ARCA to Perform Historic First Flight of Aerospike.” Press Release, 15 June 2017.