INTRODUCTION
Conflict dates to the beginning of mankind, and along with it has come the need for protective systems. Archeological records show that, from the start, humans have been trying to enhance armor for personnel, structures, and vehicles, with two seemingly opposing goals – better protection, while still being as light and unrestrictive as possible. Traditionally, better armor has often come via thicker, heavier designs and materials. But armor can become so heavy to be practically unusable. (For example, David, in his biblical battle with Goliath, eschewed the protection of heavier armor due to the weight and mobility concerns.) In addition, armor materials and enhancements must be accessible and affordable. Thus, modern-day armor developers are constantly challenged to address often-competing demands of performance, cost, weight, and space.
This article briefly summarizes work over the past decade at the Naval Research Laboratory to incorporate soft polymers in military armor and systems for civilian infrastructure protection. Because polymers are an order of magnitude less dense than steel, they are an attractive route to lighter armor. Of course, performance must also be maintained, which (as described herein) is possible by exploiting a mechanism unique to certain elastomers. In addition, cost considerations have restricted the component selection to commercially available “off-the-shelf” materials, which also expedites technical readiness.
BACKGROUND
The genesis for these efforts was a program started two decades ago by the U.S. Air Force to suppress fragmentation from buildings and similar structures when bombed. Although the foundation of a building is the primary source of its strength, fragmentation (concrete and wood fragments propelled by the blast) is the second leading cause of injury when a structure is bombed. Thus, the Air Force studied how to suppress this fragmentation by applying a rubbery polymer to the walls and foundation. The coating adheres to the structure, remains intact during an explosion, and thereby suppresses flying debris. In addition to reducing fragmentation, the coating was also found (unexpectedly) to attenuate the shock wave, requiring a blast to be closer to the building to effect damage.
The material selected by the Air Force for this application was a polyurea elastomer. Polyurea coatings have been used commercially since the early 1990s, with applications including concrete coatings; repair of roofs and parking decks; and liners for storage tanks, freight ships, and truck beds. Some prominent uses of polyurea include the Boston Tunnel Project; the Incheon International airport; and the San Mateo, CA, bridge.
Subsequently, the Navy undertook a program to explore the use of polyurea coatings to protect its High-Mobility Multipurpose Wheeled Vehicles (HMMWVs) and other light vehicles from gunfire and fragmenting explosives. Although it is counterintuitive that a soft elastomer would significantly affect projectile penetration of steel, the Navy was inspired by the work of the Air Force, and polyurea coatings were sprayed onto the outer surface of armor plates attached to the vehicle’s exterior. This technology, known as “Dragon Shield,” was used to up-armor light vehicles during Operation Iraqi Freedom.
ELASTOMERIC COATINGS
A fundamental study of elastomer coatings for armor, funded by the Defense Advanced Research Projects Agency (DARPA), was initiated at the Naval Research Laboratory (NRL) in 2004. Much of the work was performed in collaboration with the developer of Dragon Shield, Dr. Raymond Gamache, then at the Naval Surface Warfare Center – Dahlgren. To understand the origin of the ballistic and shock wave mitigation, researchers tested various soft, organic polymers as coatings on the strike face of rolled homogeneous armor (RHA) or high-hard steel (HHS) substrates. The emphasis was the connection between coating performance and either the glass transition temperature of the polymer (which is a measure of the rapidity of the polymer chain dynamics) or conventional compound properties, such as hardness and strength.
The Navy carried out both blast and ballistic tests, and found that only a particular type of polymer worked well, which limited the options to a few of the hundreds of available elastomers. The key requirement was that the elastomer have segmental dynamics (the rate at which small sections of the polymer chains move) occurring in the high kilohertz to megahertz range of frequencies. This range corresponds to the impact frequency for ballistics
(estimated as the projectile velocity divided by the coating thickness), so that a resonance exists between the rate at which the armor is perturbed and the rate of motion of the molecules composing the polymer coating [1].
This resonance condition, which can be referred to as an impact-induced transition of the rubbery polymer to a glassy state, increases the hardness of the coating by three orders of magnitude and converts kinetic energy of the projectile into thermal energy (heat). The change in properties is transient; after the perturbation, the coating returns to a soft elastomeric state. The same effect is exploited generally for energy dissipation, with examples including the reduction of wet-skidding of automobile tires, the attenuation of sonar by submarine acoustic tiles, and the suppression of turbulent blood flow around arterial plaque [2].
Because polymers are an order of magnitude less dense than steel, they are an attractive route to lighter armor.
Because ballistic impacts and blast waves are extremely different in amplitude and frequency, an elastomer functioning well to defeat one threat would not necessarily be effective against another. However, the dispersion (range of frequencies of the polymer segmental dynamics) is extremely broad for the elastomers used for these applications. Thus, while the polymer is chosen so that its dispersion maximum roughly coincides with ballistic frequencies, there is still substantial energy absorption at lower frequencies corresponding to blast waves.
The breadth of the dispersion also imparts an insensitivity to temperature, at least over the range of service temperatures. At extremely high temperatures (>60 ºC), the segmental dynamics are too fast, and the resonance condition is lost. At low temperatures (below the glass transition temperature of the coating, which is approximately -50 ºC), the polymer is already a glass, and thus the large energy absorption associated with transition of the rubber is absent.
The armor designs typically consist of a surface layer of polymer (a couple of millimeters thick) over a hard substrate; the hardness of the substrate enhances the energy conversion of the coating [3].
When exposed to ballistic impact, the coatings give rise to a unique mode of failure and a limited damage zone (Figure 1). The latter makes armor designs incorporating the coatings inherently capable of stopping multiple hits. And since the polymers are nine times less dense than steel, armor can be significantly lighter while maintaining ballistic protection (Figure 2).
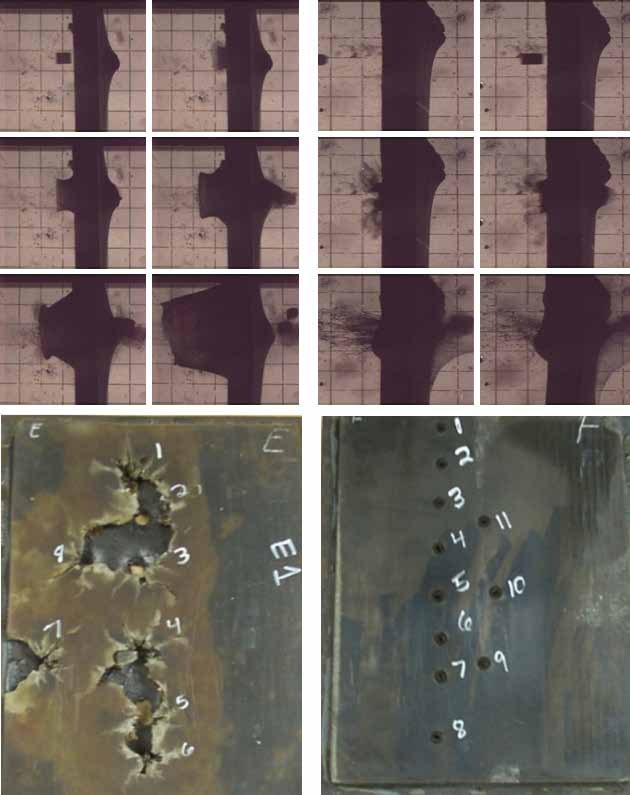
Figure 1: Elastomer-Coated Steel Substrate Impacted by a .50-cal. FSP: Conventional Rubber Stretching and Tearing (Left, i.e., images A and C); Resonating Rubber Coating Shattering Into Small Pieces on Impact (Right, i.e., images B and D); Post-Impact View of Coatings (Lower Left and Right, i.e., images C and D) (Source: NRL).
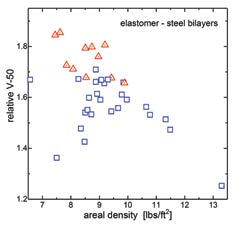
Figure 2: Projectile Velocity (.50-cal. FSP) for Which There Is a 50% Probability of Complete Target Penetration (Normalized by the Values for Conventional Steel Armor) vs. Mass Per Unit Area of the Armor: Elastomeric Polymer Coating on HHS (Squares) and Ultra-HHS (Circles) (Source: NRL).
ENHANCEMENT OF BILAYER DESIGN
The simple arrangement of a polymer coating over a hard substrate works well. However, protection from higher-severity threats can benefit from certain modifications. For example, if the projectile mass and/or velocity are extremely high (e.g., the STANAG 4496 Fragment Impact Test), equivalent ballistic performance can be achieved with lower areal densities by replacing the homogeneous coating with multiple layers of rubber on thin metal sheets [4]. This laminate construction can be used in a multiple-ply design in combination with more than one coating/steel layer.
The elastomer coating functions by being rapidly compressed, but this mechanism is effective primarily against blunt projectiles (e.g., fragments and ball ammunition). Projectiles having sharp ogives (e.g., armor-piercing [AP] bullets) cut the coating, reducing its ability to absorb energy. Thus, for defeat of such projectiles, it is necessary to rotate or blunt the tip. This rotation/blunting can be accomplished by incorporating ceramic spheres within the coating. The spheres rotate the incoming projectile, which is simultaneously eroded by the ceramic [5, 6].
The usual limitation in the use of ceramics is their weakness in tension. This weakness causes the tensile wave reflecting from the back surface of the armor to shatter the ceramic, requiring use of thicker ceramic layers to achieve sufficient erosion of the round. However, because the resonating polymer maintains its mechanical integrity, it contains the (now granulated) ceramic. Ceramic powder is effective in eroding metal, and thus subsequent incoming bullets can be defeated. Figure 3 shows a thin sheet of Kevlar added to the front surface to help maintain the granulated ceramic in place. The construction was able to pass the STANAG 4241 Bullet Impact Test, which involves three closely spaced .50-cal. AP rounds at an 850-m/s strike velocity. Note that the dimensions of the armor can be much smaller than designs relying on perforated plates to rotate projectiles.
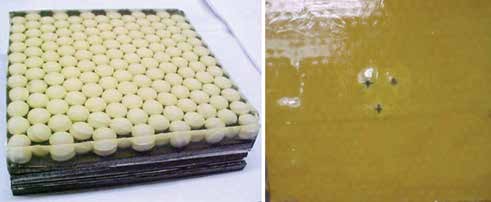
Figure 3: Ceramic Spheres Embedded in Elastomer (Left); Front-Side After Penetration by Three 0.50-cal. AP Rounds Falling Within 2-inch Circle (Stanag 4241 Bullet Impact Test), Showing Small Holes in Kevlar Top Layer (Right). The Damage Zone Is Less Than the Bullet Diameter Because the Elastomer Contains the Ceramic Granulated by the Projectile (Source: NRL).
INFRASTRUCTURE PROTECTION
A self-sealing coating can be used to prevent leakage after ballistic penetration of tanks and vessels used for gas storage. Conventional elastomers seal by virtue of their high elasticity—the ability to completely recover their original shape after large deformation. However, such materials tend to fail with widespread cracking and tearing (Figure 1), so there would be no sealing of the hole from bullet penetration. This problem is avoided using elastomers that are in resonance with the ballistic impact, as they have negligible damage (Figure 1).
Self-sealing coating might be used to protect storage tanks holding gases after .50-cal. AP bullet penetration. For this application, the coating was not intended to prevent penetration of the projectile, so that the elastomer was compounded with sufficient elasticity to completely close after passage of the bullet (Figure 4). Other applications that take advantage of the coating’s combination of ballistic penetration resistance and capacity for self-sealing are currently being explored.
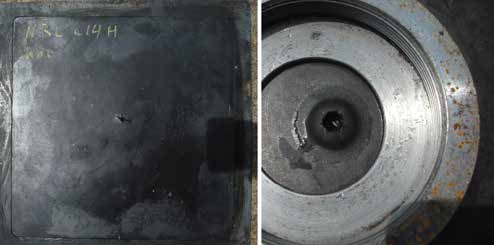
Figure 4: Elastomer Coating on Front of Steel Tank After Penetration by .50-cal. AP Round (Left); Hole in Center Has Completely Closed; Backside of Steel Vessel, With Hole Approximately 50% Larger Than Bullet Diameter (Right) (Source: NRL).
HELMETS
The high incidence of traumatic brain injury (TBI) has spurred significant efforts to modify combat helmets to more effectively mitigate the effects of a blast wave. Although the fragments of a bomb casing represent a threat similar to that from bullets, the blast wave perturbation is slower (in the kilohertz range). Consequently, there is less resonance with the elastomer and attenuated energy absorption by the coating. To enhance blast resistance, small hollow particles can be embedded within the coating to introduce another energy dissipation mechanism (Figure 5) [7, 8]. The energy lost in crushing the particles reduces the amplitude of the blast wave, which, in combination with energy absorption by the coating and partial reflection from the impedance mismatch at the helmet surface, reduces the wave reaching the interior of the helmet. Blast tests have also shown reduced displacement, velocity, and acceleration of the helmet interior (as compared to the standard Advanced Combat Helmet), along with equivalent ballistic performance and a 10% weight reduction.
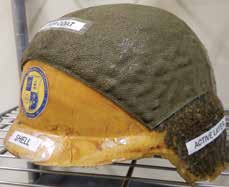
Figure 5: Advanced Combat Helmet Core With Added Layer of Resonating Elastomer Containing 33% Hollow Spheres. The Latter Have the Same Density as the Polymer, So the Helmet Weight Is Independent of Sphere Content (Source: NRL).
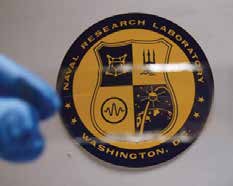
Figure 6: Transparent Elastomer Used for Coating (Source: NRL).
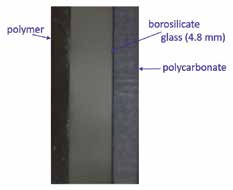
Figure 7: Representative Transparent Armor Design Used for Testing (Source: NRL).
TRANSPARENT ARMOR
Because the glass transition temperature of polymer coating is high for a rubber, its segmental dynamics are in resonance with bullet impact frequencies. Consequently, superior ballistics can be obtained with even thin coatings. For example, the V50 of HHS for a 0.50-cal. fragment-simulating projectile (FSP) increased 40% by adding a coating of soft polymer that was just a couple of millimeters thick. Because the polymer has low crystallinity, with any crystalline domains smaller than the wavelength of light, it is transparent (Figure 6). This effect suggests the feasibility of transparent armor applications, a representative configuration of which is shown in Figure 7 [9].
The particular polymer used here offers another important advantage. It is a thermoplastic elastomer, whereby its crosslinking to form a solid network is via a physical process, rather than chemical reaction. Consequently, the solidification is reversible; by heating the polymer above its softening point of 100 ºC, fracture surfaces meld together and reform. Damage can thus be repaired “on-the-fly” in the field, using a heated plate to form a new surface that is smooth and has the mechanical integrity of the original specimen. This repair capability is made possible by the coating’s ability to sustain only limited damage when impacted by a projectile (Figure 8).
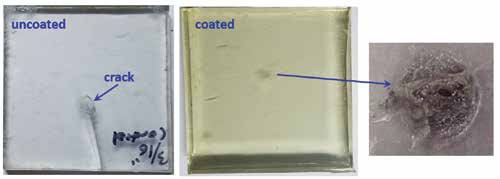
Figure 8: Comparison of Borosilicate Assembly in Figure 7: Without Front-Side Coating, Showing Crack Propagation From Impact Locus (Left); With Polymer Coating, Showing Small Damaged Region (Center); and Magnification of the Coated Target Damage (Right). The Projectile Was a Full Metal Jacket Flat Nose 9-mm + P at 1,250 ft/s (Source: NRL).
Polymer coating damage can be repaired “on-the-fly” in the field, using a heated plate to form a new surface that is smooth and has the mechanical integrity of the original specimen.
SUMMARY
As discussed, certain elastomers are able to increase the effectiveness of systems intended to mitigate ballistic and blast events. Some applications of the technology, to protect against specific threats, require custom features and are under active development. Common to these efforts (and to armor development in general) is a focus on increasing the protection level while reducing the weight. What is unique to the approach described herein is the complexity of the material response, involving not only the usual mechanical nonlinearities but also extreme rate-sensitivity of the response of polymers undergoing a transient phase transition. For these reasons, modeling has proved to be of limited value, and advancement of the technology has relied largely on testing and evaluation.