This webinar focuses on developing methods for manufacturing structural thermoplastic composite materials, characterizing the mechanical properties of such composites, and modeling the static and dynamic performance in relevant military vehicle modeling and simulation (M&S) environments. A thermoplastic polyethylene terephthalate/fiberglass composite was selected for this study due to the high specific strength of e-glass fibers, the high toughness of the polyethylene terephthalate thermoplastic, and relatively low price point, all of which made it an attractive candidate for structural lightweighting of vehicles. The raw materials were manufactured into composite laminates using a compression-molding process, and the mechanical properties were characterized using experimental test methods. Properties like stiffness, strength, and strain to failure of the composite were characterized using standard American Society for Testing and Materials methods. The resulting properties were directly fed into a computational material model. However, to characterize more complex material responses like delamination between layers, a special through-thickness, butt-joint test was utilized so the physical properties in the test matched the physics in the M&S environment. Several lessons were learned throughout the study, which may be useful to engineers and researchers looking to integrate structural thermoplastic composites into future military ground systems.
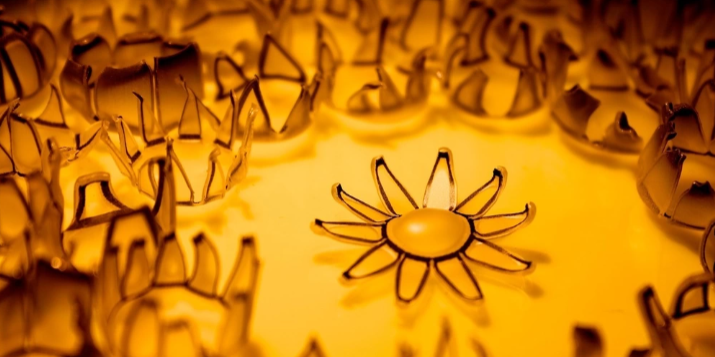
Photo by Donna M. Lindner
Presented: May 22, 2024 12:00 pm (ET)
Presented by: Evan Patton, Robert J. Hart
Focus Areas
Host a Webinar with dsiac
Are you interested in delivering a webinar presentation on your DoD research and engineering efforts?
Want to find out more about this topic?
Request a FREE Technical Inquiry!