DSIAC received a request for information on methods to better cool a high-energy, pulsed power system. DSIAC subject matter experts (SMEs) at the Texas Research Institute Austin (TRI Austin) held two teleconferences with the requestors to better understand the current system and thermal management issues. These SMEs discussed various options available, provided recommendations for potential improvements, and provided a list of reference documents from external open sources and internal TRI Austin sources. Recommendations that were made to address the overall cooling problems for the pulsed power supply include employing a higher quality thermal paste (graphene), heat spreaders/cold plates, microchannels, and/or heat sinks; increasing the thermal gradient; switching the cooling fluid; and utilizing two-phase cooling. Two-phase cooling systems that could be used are heat pipes, thermosyphons, vapor chambers, loop heat pipes (LHPs) and capillary pumped loops (CPLs), two-phase mechanically pumped loop (2F-MPL), and oscillating heat pipes (OHPs). Additionally, a directed energy SME from SURVICE Engineering delivered recommendations on other companies and SMEs in the field that might provide additional information.
Pulsed Power System Cooling
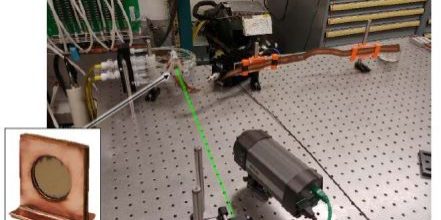
Photo Credit: UMKC
Posted on January 2, 2019 | Completed on January 2, 2019 | By: Doyle T. Motes III
What cooling methods are available for a silicon photoconductive semiconductor switch used in a pulsed power system?
Want to find out more about this topic?
Request a FREE Technical Inquiry!